Charging the energy storage system of an AGV
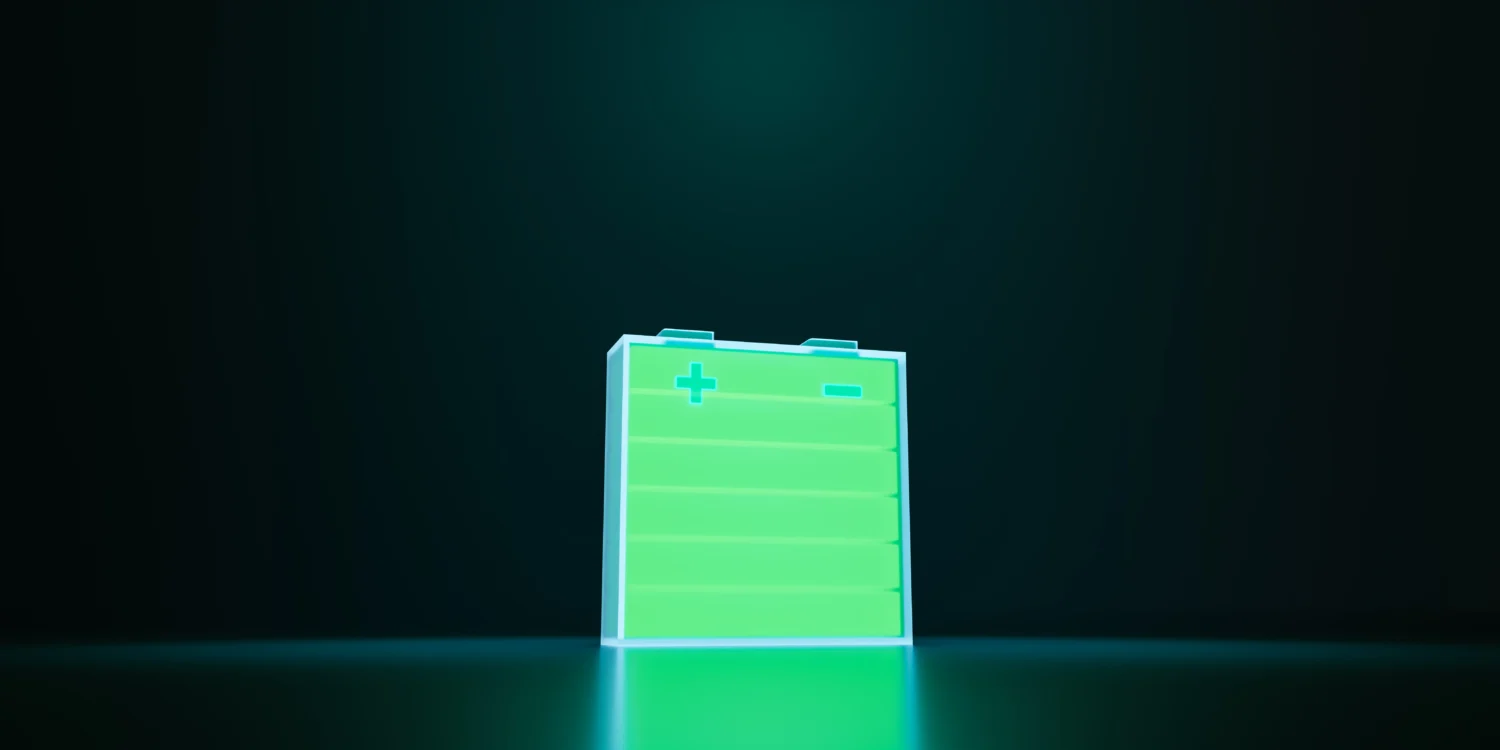
Energy storage systems are a central component in automated guided vehicles (AGVs). They make their mobile functionality possible in the first place. These storage systems, whether battery, supercap or hydrogen-based, play a crucial role in optimising the operating times of AGVs. This applies to various applications such as warehouses and production facilities. Continuous technological advances are constantly improving the power and current densities of energy storage systems. Consequently, they further drive the adoption and success of AGVs in industrial automation. Energy storage systems are indispensable key components. Furthermore, they also account for a significant proportion of the total cost of vehicles. Therefore, the charging process is of correspondingly high importance. It has the greatest influence on the service life of the energy storage system.
Energy transfer from the grid to the vehicle
Energy can be transferred from a power grid to the energy storage system via conventional charging stations. This can be done using charging or sliding contacts. It can also be done via inductive systems. While the poorer efficiency of the inductive charging process is generally likely to play a minor role, other factors must be considered. Installation and component costs, flexibility in relation to different AGV models, and the maintenance costs and intervals of the systems must be weighed up against each other.
Regardless of the transmission technology, there is always the same conflict of interest during the charging process. On the one hand, the charging process should be as fast as possible in order to minimise vehicle downtimes. On the other hand, a high charging current has a negative effect on the service life of the energy storage system. This discrepancy requires a sophisticated charging management system. It should be able to prioritise between the state of charge (SoC) and the state of health (SoH) of the storage system depending on the situation.
The basic prerequisite for such prioritisation is the ability to control the charging current and charging voltage according to the system and storage requirements. This can be done using an appropriately designed external charger. Alternatively, an onboard charger installed in the vehicle can be used. Such a charger is usually a DC/DC converter.
Controllable charging station
The great advantage of a regulated charging station is its versatility. The necessary and complex technology can be used for several vehicles. It does not have to be installed in every AGV. To avoid sparking when the vehicle makes contact with the charging port, the charger must recognise a contacted AGV. Only then should it apply the charging voltage. This prevents wear on the charging contacts and damage to the electronics. Furthermore, battery information is essential for an effective and gentle charging process. An exchange of information between the battery management system and the charging station is required.
DCDC converters as onboard chargers
When using an onboard charger, a simple unregulated AC/DC power supply unit is sufficient to supply the vehicle. There is also no need for communication between the charging station and the vehicle. If the charging process is controlled by a DC/DC converter, such as the DDL4848-48, in the vehicle, precise measurements can be taken at the energy storage terminals using sense lines. Consequently, the charging current and charging voltage can be adapted precisely to the requirements. All parameters relating to the charging process and the energy storage system are instantly available to the AGV control system via the DC/DC converter. They can be used for further process planning.
Once the DC/DC converter has recognised that there is a charging voltage present in the charging station, a delay time can be used to prevent the flow of current. This is important if the contact has not yet been fully established. By means of an integrated pre-charging circuit for current limitation in the converter, it is possible to prevent wear of the charging contacts. This wear occurs due to high current peaks and sparking during contacting.
The charging process
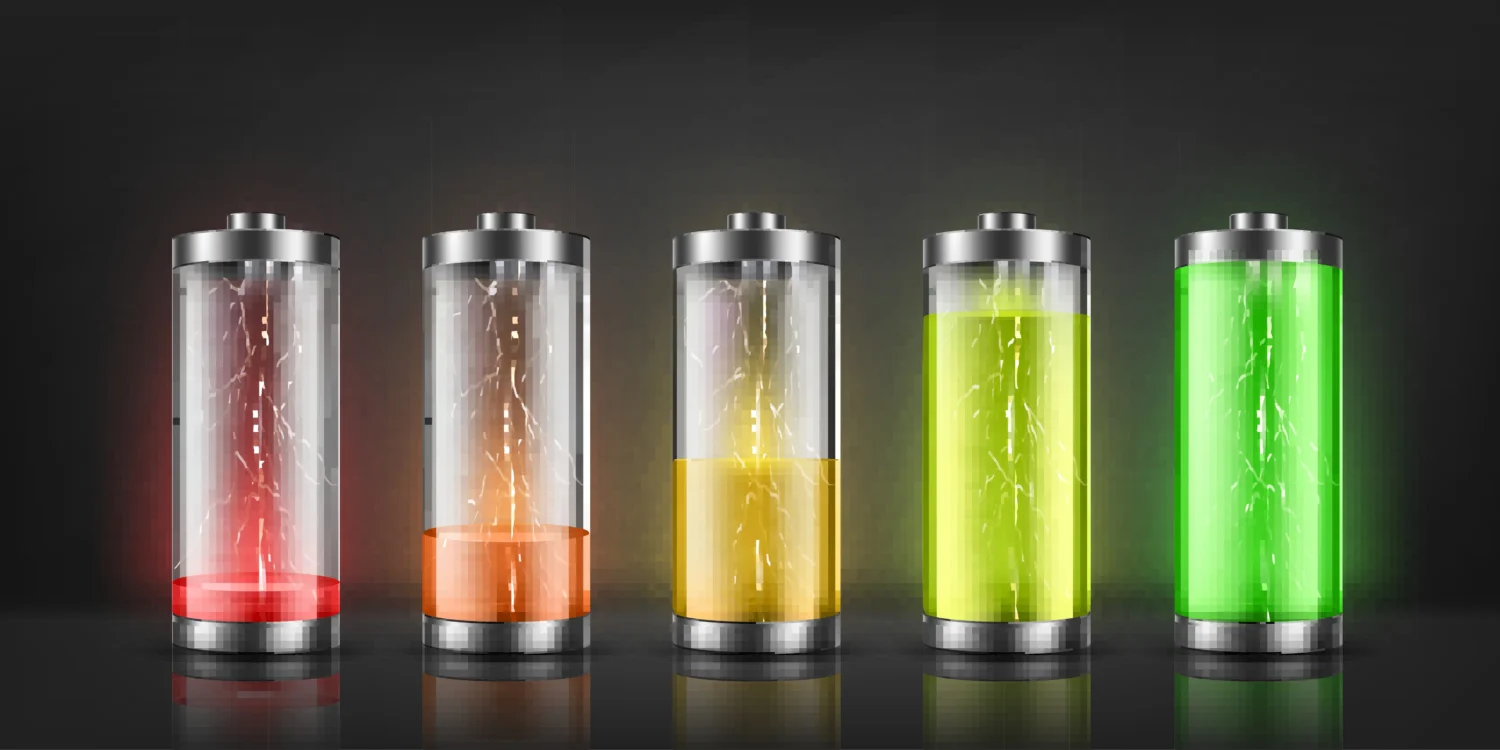
Depending on the type and structure of the energy storage system, certain charging criteria must be met. This prevents damage or even a defect in the storage system and ensures successful charging. When using rechargeable batteries, the cell chemistry, capacity, temperature and state of charge (SoC) play an important role. This SoC is not only crucial for the charging process but also for overall process control. It is decisive for the remaining time until the next charging process of a vehicle.
With lithium batteries in particular, the relatively constant voltage over large parts of the SoC makes it very difficult to determine the state of charge using voltage measurement. With the help of a precise current measurement on the installed DCDC converter, the external charger or the BMS, it is possible to determine the transferred charging energy. This is done by means of coulomb counting, i.e. recording the current over the time of the charging process. Thus, conclusions can be drawn about the SoC of the battery.
When using a supercap as an energy storage device, which has a linear voltage curve between 0V and the final charge voltage across the SoC, it is much easier to determine the state of charge. The difficulty here is that the DC/DC converter used must cover a very wide voltage range during charging and discharging.
Conclusion
Regardless of whether inductive charging or contact charging, whether external charger or built-in DC/DC converter or whether battery-electric or supercap storage, controllable current-limited power electronics are essential in all cases. Particularly in view of the importance of the energy storage system for the operation of the AGV and its considerable purchase costs, manufacturers should pay close attention to the components used.
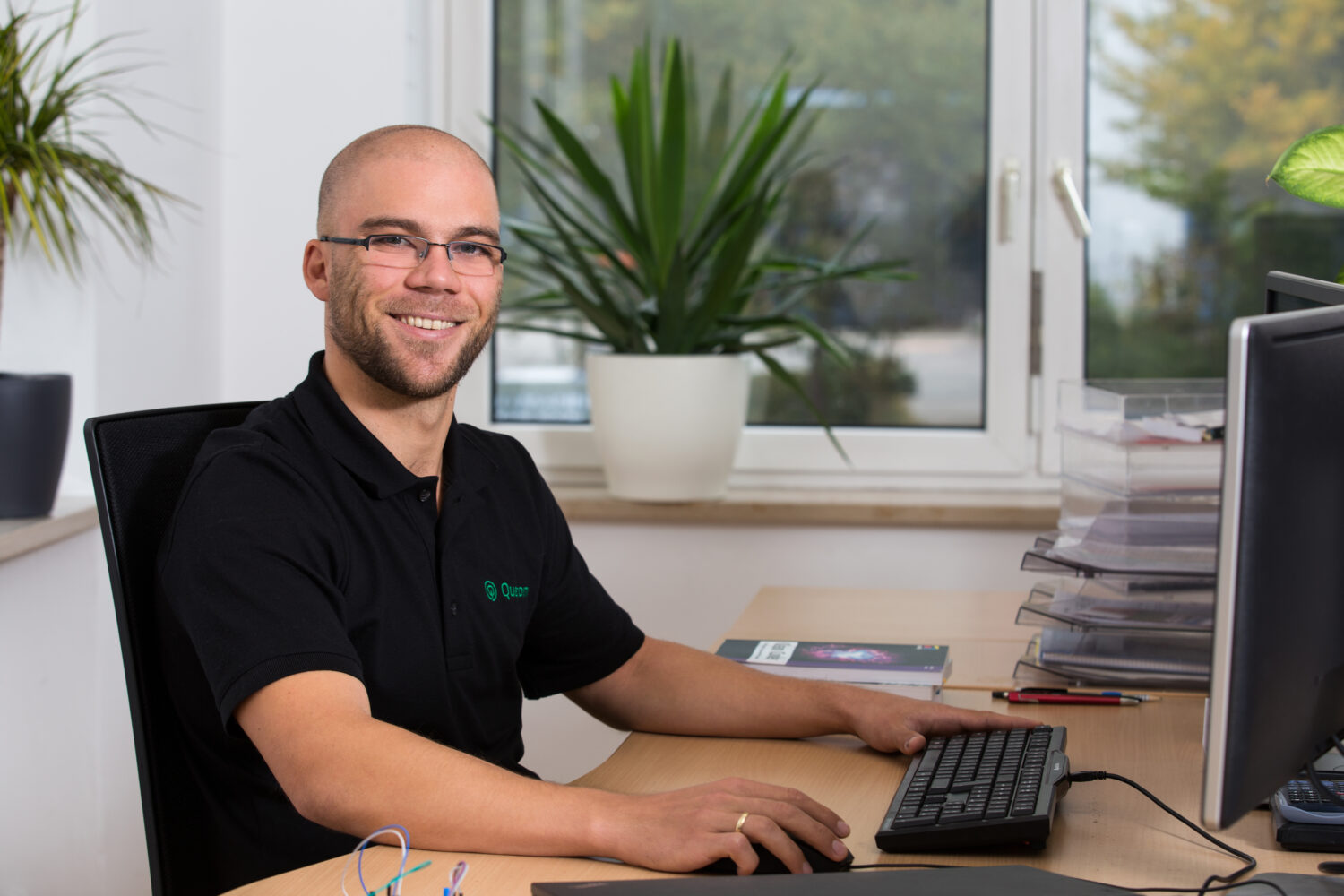
Contact
Anton Mitterreiter
Product Manager
a.mitterreiter@querom.de
+49 8743 967197-4