Power Electronics & Robotics – Status Quo & Prospects (Part 1/5)
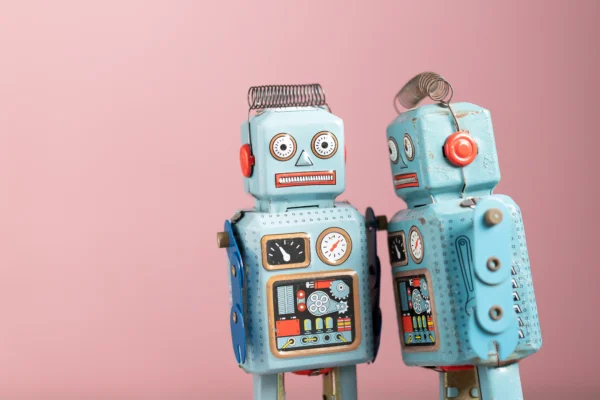
In our first article of the five-part series on power electronics & robotics, we first take a brief look at developments within the robotics industry. We highlight the role of power electronics within the technology. In the following articles, our product manager, Anton Mitterreiter, will explain in detail the energy flows that occur during the operation of an AGV. He will also discuss the key role played by power electronics.
When you think of robots, you probably think of the developments of the last 40 to 50 years. Above all, you may think of R2D2 and humanoid robots such as C-3PO from the Star Wars film series of the 1980s. However, it is hard to imagine that Leonardo Da Vinci’s first design, which can be categorised as a human-like machine, existed as early as 1495. With his “Mechanical Knight,” the multigeniuser had already laid the first foundations for robotics at the end of the 15th century.
As we know, a lot has happened since then in terms of technology. This is especially true in the field of artificial intelligence. The use of robotics in industry, agriculture, and construction, but also in social areas such as care and catering, is becoming increasingly important. Furthermore, in view of the current global political situation with wars in Europe and the Middle East, robots are also being used more and more frequently in the military sector. This includes tactical training or, for example, in the form of drones in direct use in war zones.
Before we take a brief look at these developments, let’s take a look at the categories into which robots are actually categorised.
The International Federation of Robotics (IFR), the international umbrella organisation of robotics associations and industry worldwide, based in Frankfurt am Main, divides robots into two categories.
Industrial Robots:
Automatically controlled, programmable multi-purpose manipulators, programmable in three or more axes (Def. ISO). These are mainly used in the manufacturing industry, such as the electronics and automotive industries.
Service Robots
Robots for personal or professional use that perform useful tasks for people or devices (Def. ISO). Used in intralogistics (known as AGVs/AMRs), healthcare, hospitality and agriculture.
Asia leading in the field of industrial robots
The largest and top-selling manufacturer of industrial robots by revenue in 2022 was the Japanese company Mitsubishi Electrics. They had an annual revenue of EUR 10.8 billion in the “Industrial Automation Systems” segment. In Europe, KUKA was the leader in 2022 with a turnover of 3.9 billion. They installed 300,000 units worldwide. According to the IFR, 2022 was a new record year with a total of 553,052 units. Most installations were recorded in the electronics and automotive industries in particular. In an international comparison, most industrial robots are implemented in China. Meanwhile, Germany ranks fifth after Japan, the USA, and South Korea.
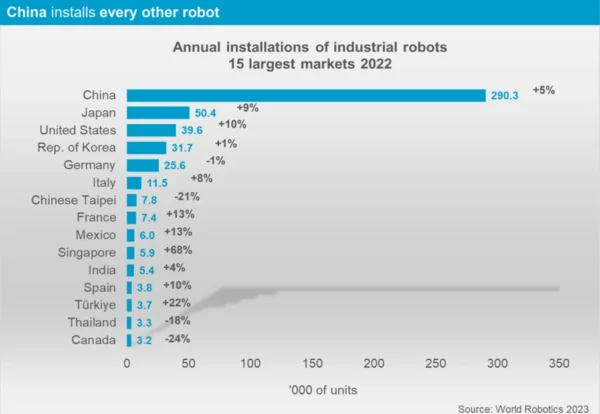
Service robots and the “robots as a service” model
In a study conducted by BCG (Boston Consulting Group) in 2021, the management consultancy pointed out that the service robot market is estimated to grow at an annual rate of 25% – 35%. This growth is between 2020 and 2023. The market will already have a volume of 90 to 170 billion US dollars by 2030.
The global shortage of labour in industry and other sectors, which we are already experiencing today, is leading to an increasing demand for professional service robots. Due to the demographic development in many industrialised countries, there will be an increased use of service robots in various areas in the future.
The resulting “robots as a service” business model, combined with technological advancements and the use of AI, will open up many new sectors.
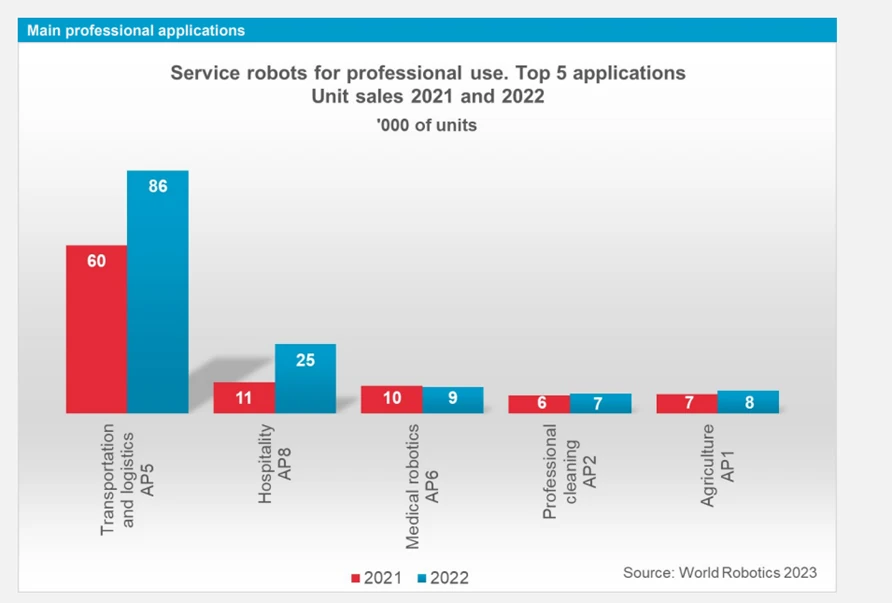
But what exactly is an AGV?
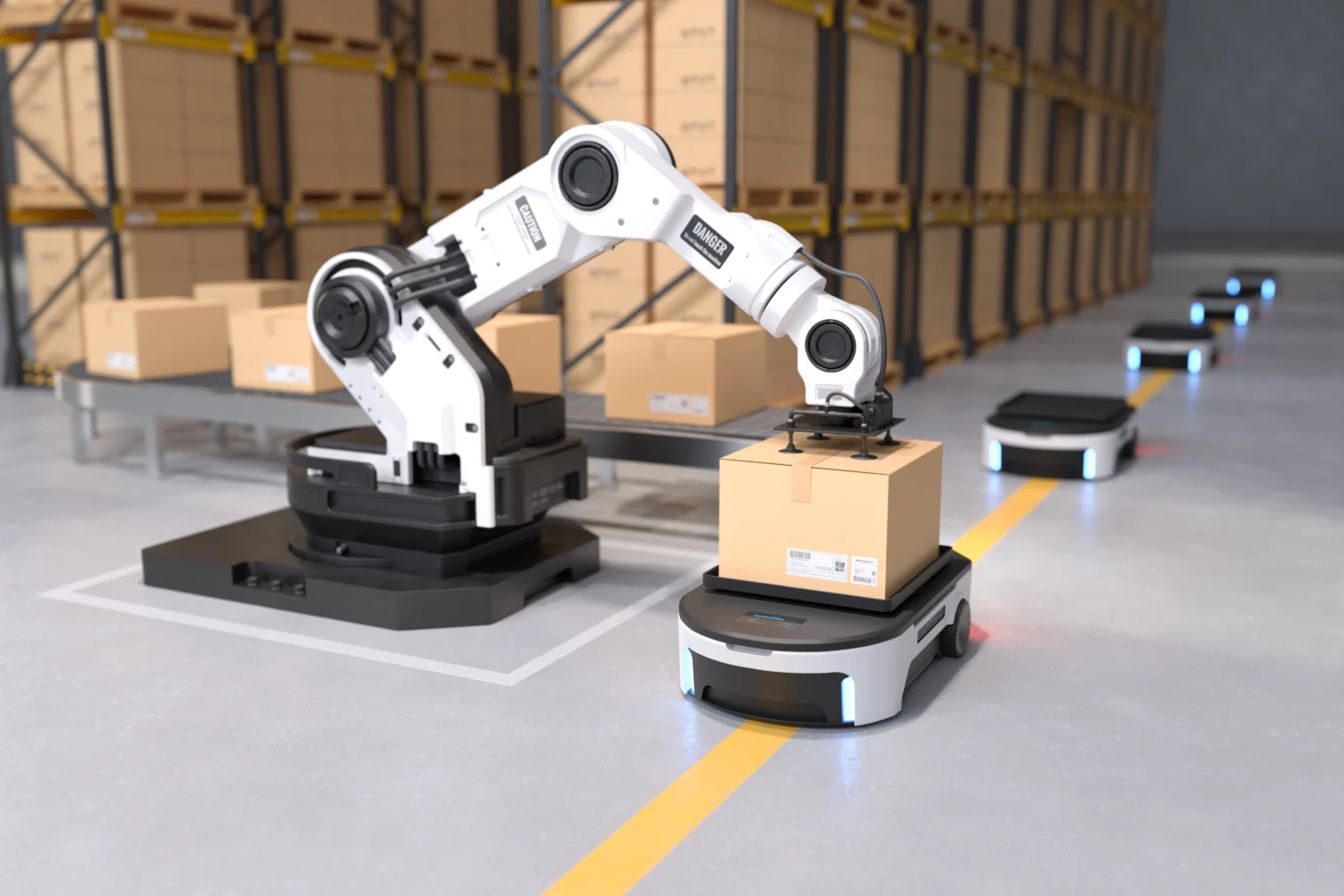
An AGV (Automated Guided Vehicle) is a robot that is primarily used in intralogistics. It transports products, parts, or parcels from A to B in large warehouses or high-bay warehouses, for example. An AGV basically consists of five hardware components with the following tasks:
- Vehicle platform: Basic structure of the AGV.
- Motion system: Components for movement, e.g. motors, wheels, mast.
- Power System: Energy storage and power electronics.
- Control System: Central control system.
- Navigation System: Responsible for directional guidance, e.g. laser, wire, magnet.
In recent years, more and more AGV manufacturers have evolved from pure manufacturers focussing on hardware to system integrators focussing on software. Technological progress in energy storage systems and the need to utilise energy more efficiently have made power electronics an immensely important hardware component within AGVs.
DC/DC converter as central energy control unit
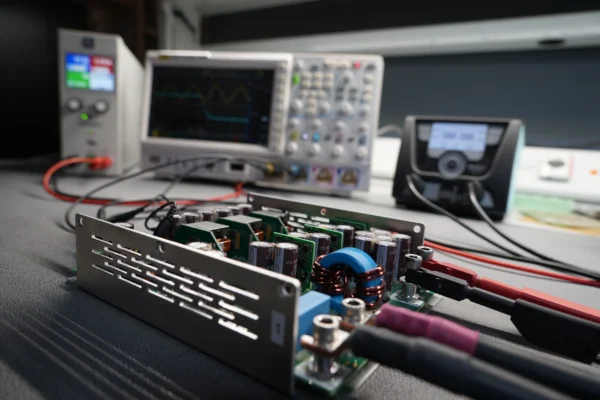
The power electronics, as one of the hardware components, plays a central role within an AGV in the form of a DC/DC converter. It has several important functions, which are briefly explained below.
Voltage conversion: The converter adapts the voltage of a source, e.g. a battery, to voltage levels suitable for the various components of the AGV.
Current regulation: By regulating the current, the DC/DC converter can ensure optimum and safe charging of an energy storage system.
Efficiency optimisation: The converter helps to improve the efficiency of energy consumption. It ensures that energy is transferred effectively from the source to the connected devices.
Isolation: Some DC/DC converters provide isolation between the various power and communication interfaces. This minimises electrical interference and ensures the safety of the electronics in the AGV.
Adaptation to variable loads: The converter helps to keep the output voltage stable with fluctuating loads. This ensures a reliable power supply.
Conclusion:
The strong growth in the robotics sector remains unchanged. Robots are indispensable, whether in an industrial or social context, particularly in view of the shortage of skilled labour and demographic trends. Power electronics play an important role within service robots, as they fulfil important functions as the central energy control unit.
In the second part of the Power Electronics and Robotics series, our product manager Anton Mitterreiter explains the challenges and opportunities involved in transferring energy from the grid to the vehicle’s energy storage system.
If you have any questions, please feel free to contact us at any time.